"We have a viscous liquid, which means a volumetric pump: screw, gear, peristaltic, diaphragm... Everything is obvious here, we have a pump, we have its characteristics, and we can confidently choose the right unit," the customer replied without hesitation.
This is not a new topic, but since the same questions arise every time, let's look at it in more detail. To begin with, it is necessary to understand what viscosity is and what types of viscosity exist.
What do we know about product viscosity?
Viscosity describes the fluidity of a liquid. High viscosity fluids are thick fluids and low viscosity fluids are thin. This viscosity is the result of intermolecular forces, also known as internal friction. This internal friction decreases with increasing temperature and increases with decreasing temperature.
In a nutshell, to save you time, here are the things to consider when choosing a pump for viscous liquids:
- viscous media means anything that cannot be handled by a centrifugal pump, i.e. above 200 cSt;
- each pump has its own limitations in terms of ultimate viscosity and different viscosity loss factors during pumping;
- some products may not have any fluidity at all, such as minced meat, but it can still be pumped;
- the chemical composition of the viscous fluid is important when selecting the flow part of the pump;
- viscous media often solidify and have a high density.
The thicker the liquid, the more difficult it is to pump?
The viscosity or "thickness" of a fluid certainly has an impact on its behaviour in a pump, because the viscosity of a fluid can change under different conditions. There are four main groups of liquids, each of which behaves in a certain way despite its specific viscosity.
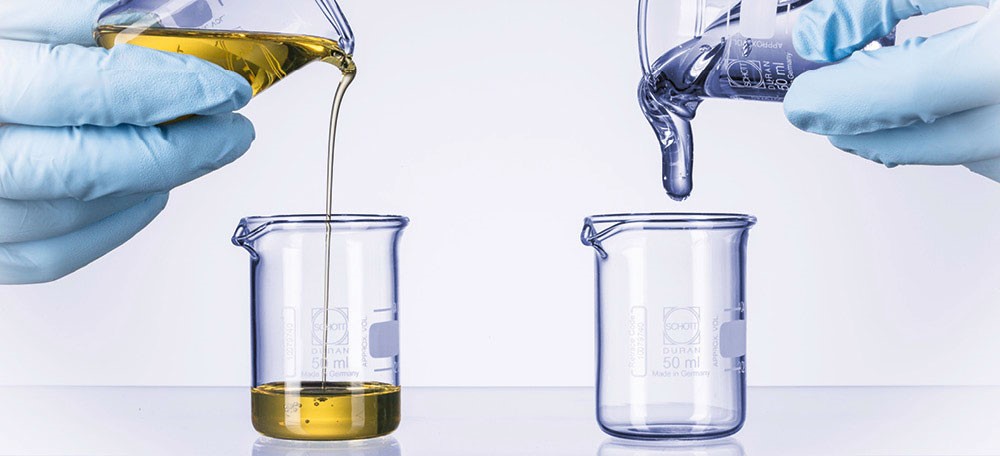
Firstly, when pumping liquids such as water, alcohol and paint thinner, it doesn't matter how fast they are moving because they all flow the same way.
The second type is "dilatant fluids", in which the viscosity increases with increasing shear strain rate. The dilatant effect is observed in materials in which densely packed particles are mixed with a liquid that fills the space between the particles. At low shear rates of the material layers relative to each other, the liquid acts as a lubricant, and the dilatant material is able to flow easily. At high velocities, the fluid does not have time to fill the free spaces formed between the moving particles, and therefore the friction between the particles increases greatly, leading to an increase in viscosity. For example, cream and butter, the viscosity of which increases during shaking until it becomes almost solid. They cannot be pumped, for example, in standard centrifugal pumps and require special measures to move them.
Thirdly "plastic liquids" have a yield point (resistance point) that must be exceeded before they begin to flow. After that, the viscosity decreases as the agitation increases. The best example of a plastic liquid is ketchup. Think about how you have to shake it in the bottle before it starts to move? But when it does move, it flows easily.
The fourth group, "thixotropic liquids", is the most difficult to explain... and to deal with in pumps. This category includes glue, non-drip paints, lubricants, cellulosic compounds, soaps, starches and tar. These liquids become viscous (thick) when they stand, but they will eventually become less viscous (more liquid) with constant agitation.
Based on the above, there are two types of viscosity - dynamic and kinematic...
The so-called "kinematic viscosity" is a real physical factor that affects the performance of the pump, so you need to be aware of it. The kinematic viscosity is specified in centistokes (cSt) and is measured in mm2/s. For example, water has a low viscosity of 1 cSt at 20 °C, while engine oil has a higher viscosity of over 500 cSt at the same temperature.
Viscosity is essentially resistance to flow, and it matters for pumps. If you have a sticky, high viscosity liquid on your hands, it sticks and is much harder to remove than a low viscosity liquid. The same goes for the pump. If you are pumping liquids, such as engine oil, that stick to the surface of the impeller, this is a problem that needs to be considered.
In addition, each viscosity has a density.
Different liquids can have different densities (or weights, measured in g/cm3 or kg/m3), and the density of one type of liquid depends on temperature.
When we size pumps, we pay particular attention to the "head", i.e. how many metres in the air we can pump a given liquid at a pressure of one bar. Heavier liquids require higher pressures to pump.
So what is important to pay attention to when pumping viscous liquids?
Now it's time for a concrete example. Let's take a look at pumping a heated condensed liquid with a viscosity of 6000 cSt with a flow rate of 5 cubic metres per hour and a pressure of 2 bar. This will be a pump with nozzles most likely 50 mm in diameter.
Let's say the pump is selected with the recommended speed. And now let's talk about something that you probably forgot to take into account. The condensed milk will be pumped through pipes, the length of which is usually neglected, as well as the turns of this pipe, and the material from which this pipe is made. This is where the problem begins. The fact is that the walls of the pipeline through which the product flows create resistance to the product's movement due to the roughness of these walls. So, in our example with condensed milk, if the pressure pipe from shop to shop without bends and rises is 30 metres long and made of polymer with seamless welding (ideal conditions), then in order for the product to flow through it at a rate of 5 cubic metres per hour, it is necessary to maintain a pressure of more than 16 bar. This is the wall resistance loss in this case. An unexpected twist: 16 bar is a very large figure, which is not as critical for condensed milk as it is for ketchup with chunks. And you need a pump with a large and powerful drive. In other words, an expensive one!
The most rational solution is to increase the diameter of the pipeline. So, for example, in our case, if the pipeline diameter is doubled to 100 mm, the pipeline losses will be only 1 bar, while for a 75 mm diameter pipeline, these losses are slightly more than 3 bar. And this is a completely different pump. There are fewer zeros in its cost and the cost of its consumables.
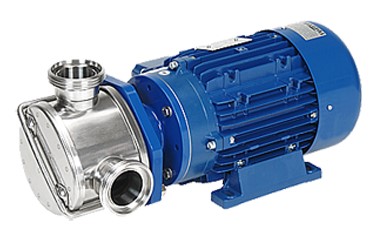
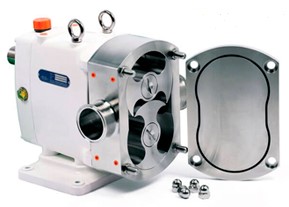
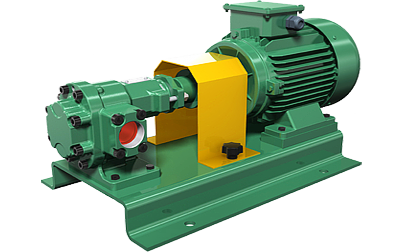
And finally!
There are no universal pumps, you always need to choose a model for a specific task.
Our specialists will be able to select pumps for viscous liquids based on your application. Set a task for an engineer right now: +380 44 3907338 and provide your production with safe and reliable equipment for many years.