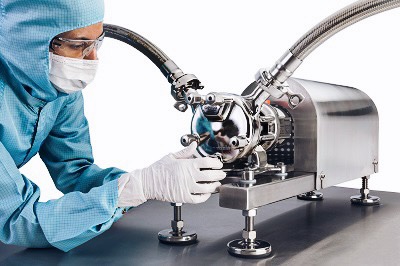
Today, the pharmaceutical industry is going through a period of significant change. The COVID-19 pandemic has accelerated the development of new vaccines and medicines in record time. We had to admit that it is unlikely to be possible to quickly develop and launch new drugs using old equipment. And the pharmaceutical industry is considered to be lagging behind in terms of innovation. Technology has hardly changed for decades. In fact, pills are now produced in the same way as they were 50 years ago. In addition, innovative drug developers are proposing treatments that fundamentally change the way they are produced. The root of the problem is that 99% of the technologies were previously developed through trial and error.
As a result, the methods used today require high costs to ensure the proper level of product quality, but this does not prevent the appearance of defective batches of products and losses of raw materials. Moreover, the transition from small pilot batches to large-scale production is often hampered by a number of unforeseen scale-up issues that can cause delays and supply shortages, as well as lead to excessively high associated costs. A rational, scientific approach to production is pharmaceutical engineering, which, based on fundamental knowledge of materials and technology, allows us to predict product quality and production features. The pharmaceutical industry and regulatory authorities understand that changes are necessary, so some progress is being made.
Despite all the challenges we face, we are optimistic about the future with our modern technical solutions and knowledge. Continuous manufacturing, single-use technologies and other innovations that can help reduce the cost of pharmaceutical production and make it more flexible are starting to gain momentum. Of course, the pace of change is not as fast as we would like, but there is no doubt that we are moving in the right direction.
What does the pharmaceutical industry have in store for the near future?
New trends, new technologies... We believe that in order to accelerate progress, it is necessary to develop more reliable production processes and strengthen cooperation between drug manufacturers and technology developers. This will allow us to obtain innovative technologies that meet the current requirements of the industry.
As experts, we are familiar with the needs and nuances of pharmaceutical processing plants and benefit from long-term relationships with trusted equipment manufacturers. Today, we know for sure that the continuity of production depends to a large extent on the reliability and efficiency of pumps. It should be noted that the larger the pharmaceutical company, the more powerful pumping equipment it needs.
When buying industrial pumping equipment, you should have a clear understanding of its features. As a rule, it is used for pumping contaminated and aggressive working media with foreign inclusions, as well as for working with clean water. In this regard, the internal equipment of industrial pumps and pumping stations is often exposed to increased physical and chemical stress, which makes it prone to mechanical damage and premature wear. For this reason, this type of equipment is manufactured using particularly durable materials and alloys to minimise the risk of breakdowns, as well as special seals and thorough lining of the inner surface of the flow channels.
Steiner Ukraine, which has been successfully supplying industrial pumping units and components to the Ukrainian market since 2006, offers pumps and pumping stations from international manufacturers who are technological leaders in the field of industrial pumping equipment.
Centrifugal pharmaceutical pumps are industrial units in which the mechanical energy of the drive is converted into hydraulic energy of the liquid, resulting in its movement. Pumps in this category are one of the main types of equipment that ensure an uninterrupted and continuous technological process at pharmaceutical companies. This equipment is designed for pumping liquid media with different physical and chemical characteristics, at a wide range of temperatures.
If you need to buy a pharmaceutical centrifugal pump, please note that special requirements are imposed on this equipment, as it must ensure maximum sterility and hygiene of all processes taking place inside the unit. This is the only way to guarantee the high quality of the final product produced by these industries.
Design of centrifugal pharmaceutical pumps
The main element of the pump is the electric motor, which acts as a driving device. In order to protect the power unit from any contact with the pumped liquid, the internal structure of the pump, in which the drive motor is located, is properly sealed. Rotation is transmitted by the pump shaft from the electric motor to the impeller(s), on the outer cylindrical surface of which the blades are placed, which are responsible for moving the pumped liquid in the internal chamber of the unit. The easy and trouble-free rotation of the shaft on which the impeller/wheels are mounted is ensured by bearing assemblies. All components of the pump's internal structure are protected from dangerous contact with the liquid medium by special sealing elements. The casing of the unit itself resembles a snail in appearance and is equipped with two more elements - a suction nozzle and a discharge nozzle.
The principle of operation of centrifugal pharmaceutical pumps is extremely simple: the liquid entering the internal working chamber is captured by the impeller(s) and starts moving with them. The centrifugal force throws the liquid against the walls of the working chamber, which creates an overpressure that pushes the moving liquid further out through the discharge pipe. When the liquid is thrown against the walls of the working chamber, a region of discharged air is created, which ensures that a new portion of liquid is sucked in through the suction nozzle.
Advantages of centrifugal pharmaceutical pumps over other types of pumps:
- stable high performance indicators, which are ensured by the principle of operation of these units and their design features;
- stable flow parameters of the pumped liquid;
- ease and simplicity of operation of the centrifugal pump, as well as its independent maintenance - there is no need to involve third-party personnel, and all necessary maintenance and repair procedures can be carried out using basic tools with certain skills;
- the reliability and low wear and tear of centrifugal pumps, and as a result, their long service life;
- the relatively low weight of this type of pump and its compact dimensions;
- for the production of pharmaceutical pumping equipment, we use clinically tested alloys that are not subject to any kind of corrosion, and carefully studied polymers and plastics that are safe for the human body and the environment, as well as resistant to aggressive chemical compounds and reagents.
There are also disadvantages to centrifugal pharmaceutical pumps
In order to make the right choice of pumping equipment used in industry, it is necessary to have a clear understanding not only of its advantages, but also of some of the disadvantages of centrifugal pumps:
- the inability to remove air voids from the suction line without additional special equipment;
- when deviating from the nominal operating conditions of this type of pump, their efficiency is significantly reduced;
- direct dependence of efficiency on the viscosity of the pumped liquid - the higher the viscosity, the lower the efficiency;
- this type of pumping equipment is not ready for operation until a liquid medium is created in the internal working chamber;
- centrifugal pumps with more than one impeller should be used in the system to create a high head of the pumped liquid;
- a relatively limited range of pumped fluid flows and heads within the system;
- relatively high price due to the use of high-quality materials for the pump's working parts.
We offer pharmaceutical centrifugal pumps from the world-renowned manufacturer Packo (Belgium) with proven product quality. Our experts will help you choose the right pump based on your requirements and application. You just need to prepare a list of the necessary parameters and requirements that the equipment must meet, and we, in turn, will provide the most reliable and profitable options.
In addition, our service engineers perform maintenance, warranty and post-warranty service and repairs of pumping equipment. Our technicians are regularly trained and refreshed at the manufacturers' plants.
Steiner is your reliable partner for industrial pumping technology!