In this article, we will talk about eccentric screw pumps, one of the most famous and widespread pump groups. The principle of the screw pump was discovered in the 1930s in France, when French scientist Dr Rene Moineau patented his invention of a gearbox using a helical rotor inside a spiral cavity. Later, the principle of the gearbox became the basis for these pumping units. Today, when Muano's patent has expired, many companies use and refine the technology for the production of screw pump units. This type of pump has found its application in a wide variety of industries: chemical, oil and gas, pharmaceutical, and food production.
The principle of operation of a screw pump.
A screw pump consists of a screw rotor that rotates inside a screw stator. The metal rotor is manufactured to a high degree of precision, while the stator is moulded from a resilient elastomer. The geometry and dimensions of these parts are such that when the rotor is installed in the stator, a double chain of sealed cavities (cells) is created. As the rotor rotates in the stator, the cells move in a spiral along the pump axis, changing neither their shape nor their volume. The elements of the screw pair fit tightly together, which ensures even proportional pumping with minimal backflow. The contact between the rotor and stator also determines one of the most important features of screw pumps - the ability of the same unit to deliver a constant pressure at different rotational speeds. This feature has made screw pumps very popular in dosing and proportional flow applications. A schematic representation of the main components of a screw pump is shown in Figure 1.
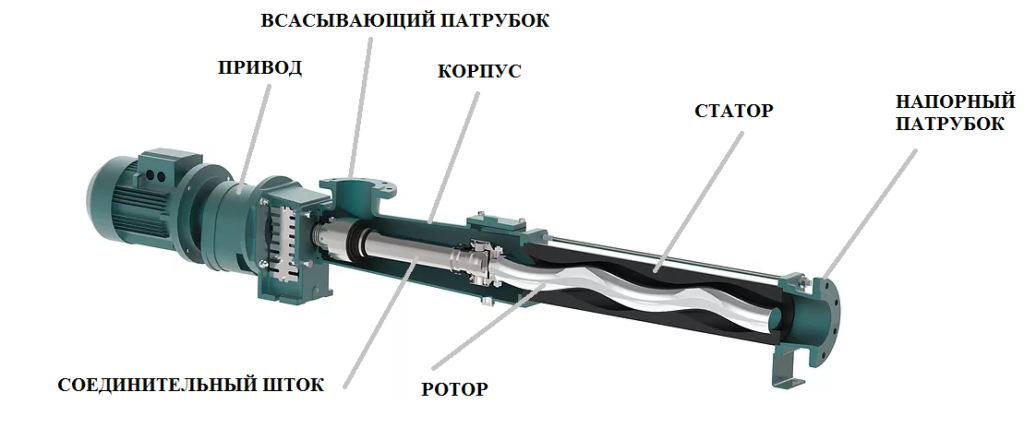
Design features and versions
Depending on the requirements of the process, screw pumps can be designed in a wide variety of ways. Based on the model range of our Italian partner Sydex Srl, the following are the possible variants of screw pumps:
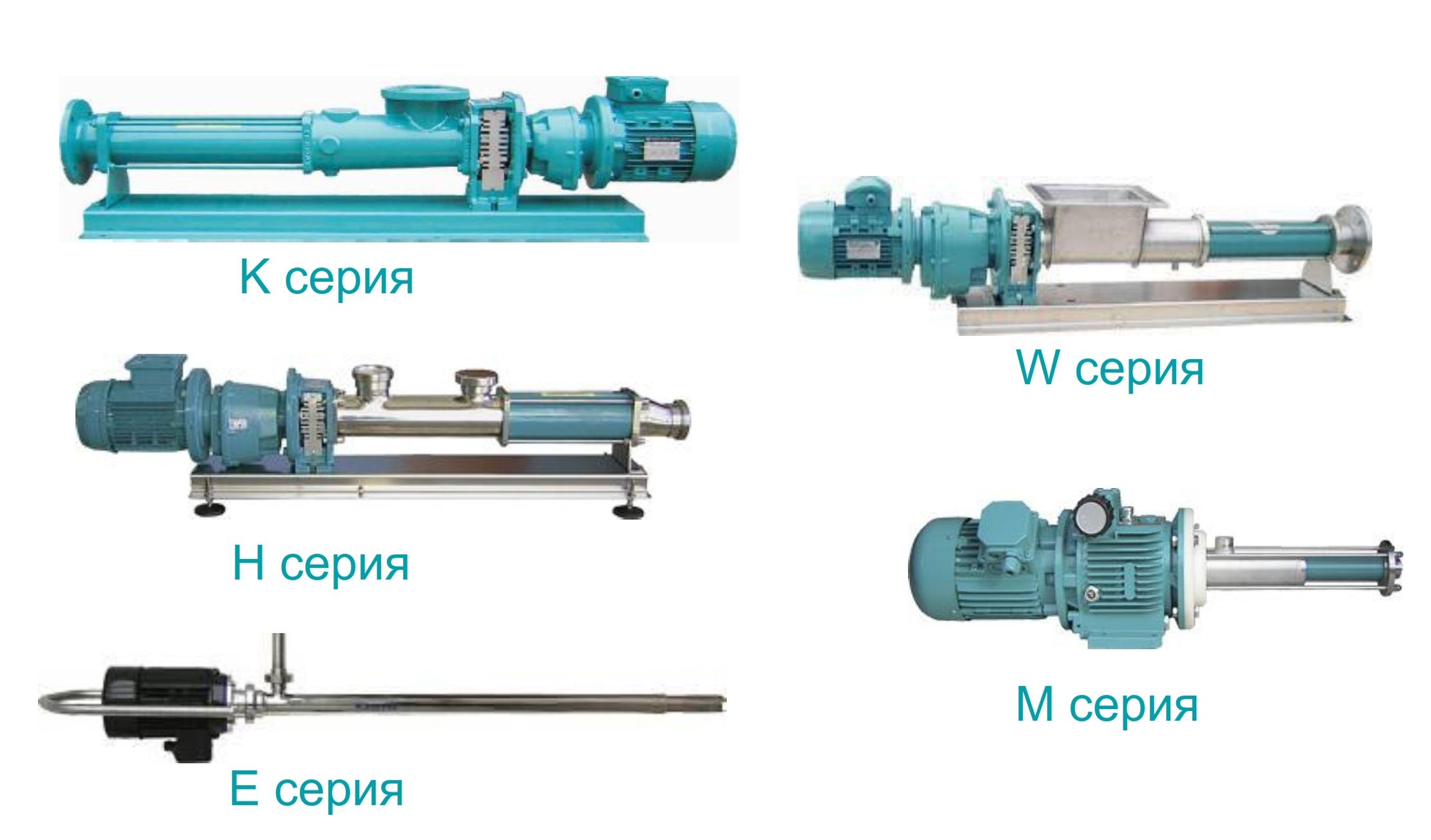
K-series. The most widely used general industrial series, high efficiency and many material options.
H-series. A series specially adapted to the needs of the food industry, where hygiene and sanitary performance are of the utmost importance. Adaptable for SIP sinks, FDA and EHEDG compliant.
E-series. Special design for vertical installation and pumping products from containers and drums.
M-series. A special series for precise dosing and proportional feeding. It can operate in the speed range from 0 to 1000 rpm, with an integrated frequency converter.
W-series. It is designed for particularly viscous, high-suspended solids or non-flowing products. For such applications, a special storage hopper is provided on the suction side of the pump, as well as a feed screw that forces the product into the rotor and stator chamber.
In addition to the design of the pump unit itself, one of the most important considerations is the geometry of the screw pair. It determines the pressure, the volume flow rate, and the intended use for a particular product. Below are some possible screw pair configurations:
"S" geometry:
- very smooth feeding
- compact dimensions despite the large number of steps
- large cross-sectional area of the entrance
- low flow rate/high suction capacity
- pumping of compressed particles is possible
- pumping of large particles

"L" geometry:
- good volumetric characteristics with a long overhaul period due to the long contact line between the rotor and stator
- compact dimensions with high performance
- lower friction speed

Geometry "D":
- very small dimensions with high pressure and performance
- almost pulsation-free pumping
- high dosing accuracy

Geometry "P"
- compact dimensions with very high performance
- almost no pulsation
- high dosing accuracy
- good volumetric performance, long overhaul period due to the long contact line between rotor and stator.

Screw pumps in dairy production.
The possibilities of screw pumps could not go unnoticed by the dairy industry, which is full of challenges in its pumping processes. The most popular products that can be transported with a screw pump are yoghurt, sour cream, cream, fruit fillings, processed cheese, whey, condensed milk and others. One of the most important qualities of a screw pump is the ability to handle viscous products gently. The level of hydraulic shear in a screw pump is minimal - the pumped medium is gently and linearly pushed along the screw pair. For some dairy products, excessive dynamic impact is detrimental and has a negative impact on their further functionality in the process. In addition, the design of the screw pump allows for hygienic operation, i.e. adaptation to the cleaning system, use of food-grade materials, and no stagnant zones. Also, screw pumps are very easy to use and control the process they are involved in. All this is due to the proportional flow rate and stable pressure.
To summarise, the following advantages of screw pumps for dairy production can be highlighted:
- hygienic design
- the ability to work in a closed loop
- easy washing and cleaning
- easy disassembly and dismantling
- stable delivery pressure regardless of rotor speed
- work with viscous products
- gentle pumping of sensitive and delicate products
But despite all of the above positive qualities, there are a few disadvantages, such as the overall dimensions and relatively rapid stator wear. The latter is a problem that directly depends on the operating conditions, the quality of the stator and the accuracy and quality of the pump assembly. If the unit is selected correctly and is of good quality, problems are expected to be minimal.
This short overview may help you to choose the right solution for your dairy products.
Steiner Ukraine specialists will be happy to help you solve your problematic pumping processes.