A diaphragm pump is a volumetric pump in which the product is pumped through the reciprocating movements of a flexible diaphragm (diaphragm). As a rule, such units are equipped with two diaphragms that operate alternately, which to some extent compensates for flow pulsations at the discharge pipe. The principle of operation is shown in the illustration below.
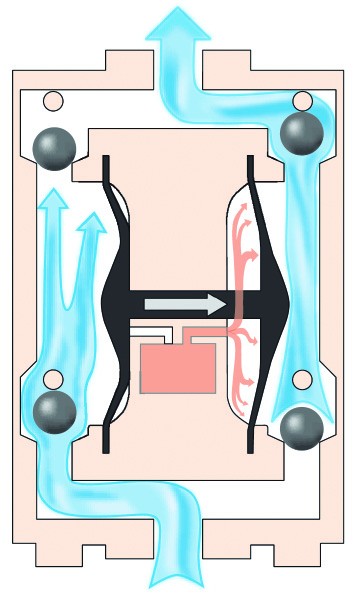
First of all, it is worth noting that the pump runs on compressed air, not electricity. The drive mechanism is a pneumatic valve, which is a unit with moving pistons and a system of air distribution channels. When compressed air is supplied to the pneumatic valve, the pistons begin to move, directing air flows to each diaphragm in turn. The diaphragms are connected to each other by a stem, so that when one is extruding, the other is retracting accordingly. As a result, while one side sucks in the product, the other side squeezes it out. The suction and discharge of the product is carried out through check valves.
Pneumatic diaphragm pumps are most widely used in the chemical, pharmaceutical and food industries, as well as in metallurgy and construction.
Depending on the process requirements, diaphragm pumps can be made of different materials: casing made of polypropylene, PVDF, aluminium, stainless steel, cast iron or Teflon. The membranes also come in a variety of designs - NBR, PTFE, EPDM, Santoprene, Hytrel, etc. Materials are selected depending on the chemical properties of the pumped medium, its abrasiveness, adhesive properties, etc.
Main features and advantages of pneumatic diaphragm pumps
- Compact and reliable design - low operating costs;
- Capable of pumping both liquid and viscous products with solid inclusions;
- No mechanical seal, so the risk of leakage is minimised
- The compressed air drive eliminates sparking, making it possible to use the pumps in hazardous areas.
- The pump can be submerged in the pumped medium
- Free work "on the dry"
- Self-priming up to 9 metres (for some models and more)
- Easy to adjust performance by changing the air supply volume
- Safety - in the event of a pressure drop in the discharge line (operation with a closed valve or when the discharge connection is blocked), the pump simply discharges the exhaust air without any damage
- Gentle pumping of the product
- Lightweight and easy to maintain
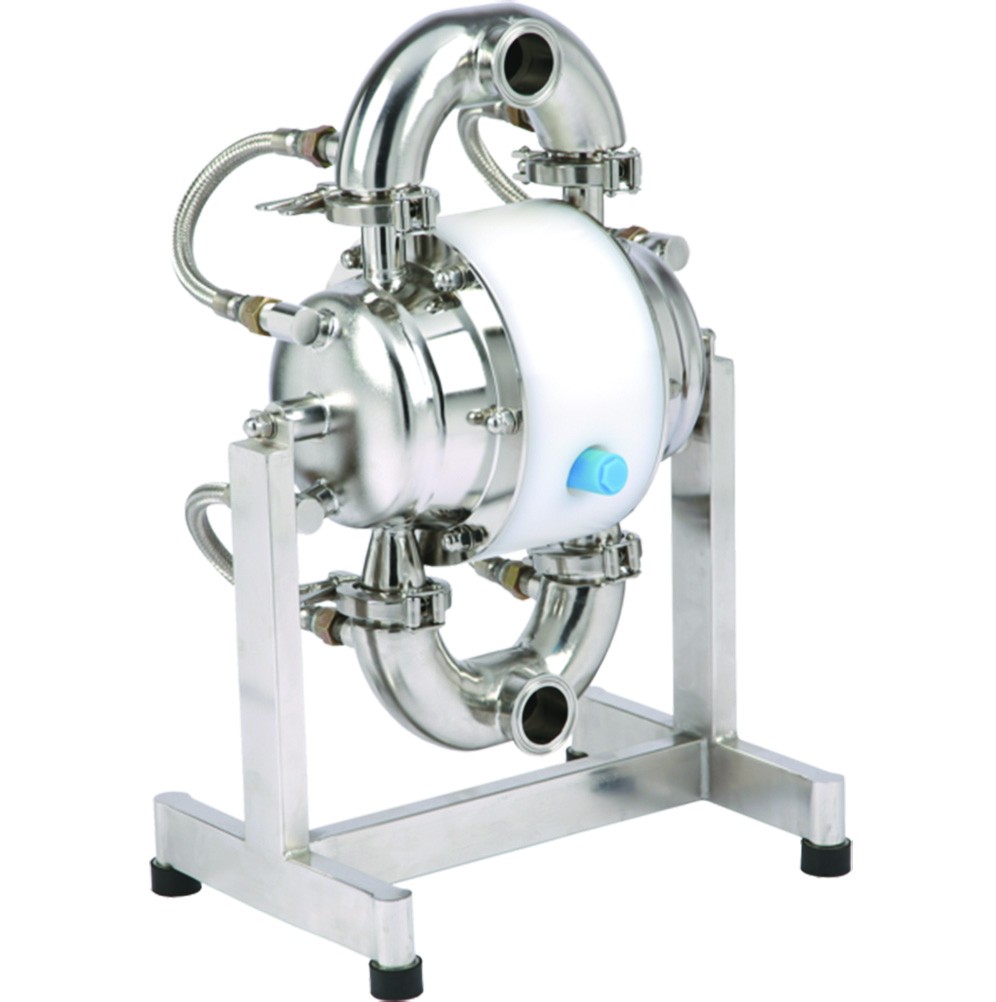
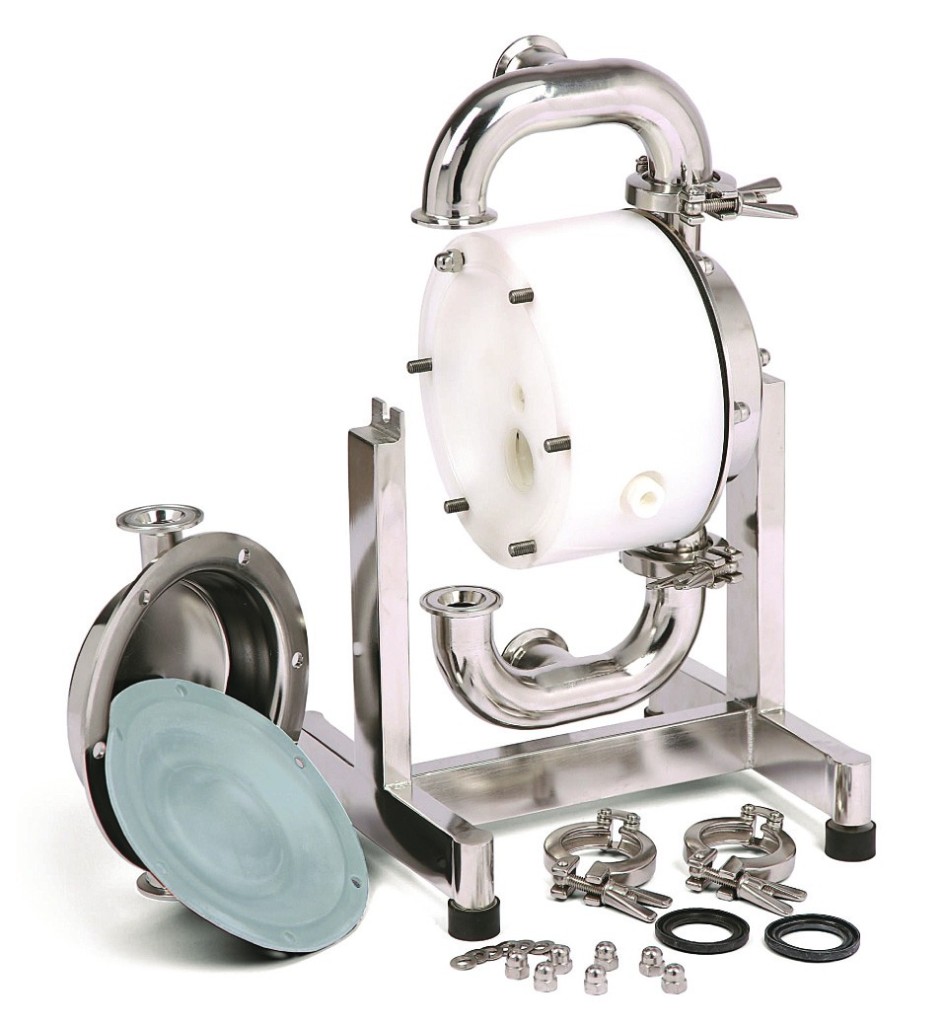
Diaphragm pumps in dairy and industrial applications
As we have discussed in our previous articles, hygienic design of equipment implies a number of requirements. Hygienic diaphragm pumps are a separate product line for each manufacturer, which requires a special approach. Distinctive features of hygienic diaphragm pumps:
- The materials of the flow part are made of AISI 316L stainless steel with a corresponding surface polishing.
- The membranes are made of food-grade materials, usually NBR, EPDM, PTFE or Santoprene. Another important point is the attachment of the membrane itself - in general industrial models, they are attached to the stem with a threaded connection. This does not quite meet the hygiene requirements, as there is a risk of harmful microflora accumulating in the gaps between the fasteners. For this reason, sanitary models of pumps use pressed diaphragms with a smooth surface and no stagnant zones.
- The geometry of the flow part without dead spots, sanitary Tri-clamp or DIN 11851 connections, sanitary design of the check valves - can be ball or petal.
In the dairy industry, diaphragm pumps can be used to pump cream, sour cream, yoghurt, condensed milk or whey-grain mixtures (in cheese production). The main feature of the diaphragm pump that makes it hygienic is the absence of a mechanical seal. This ensures ease of maintenance and tightness, as well as protection against product leakage. In all other respects, diaphragm pumps are quite convenient due to their design features: self-priming ability, dry operation, and protection against pressure drop. Another advantage is the gentle pumping of the product, which is a fairly common requirement in dairy production. The most striking example is the pumping of cheese grains in whey. In this process, maintaining the integrity of the grain directly affects the yield of the finished product. If the pump has an excessive destructive effect on the sensitive solid fraction, the so-called "dust" is formed, which goes along with the whey after it is separated. According to our customers, a diaphragm pump is the most optimal solution for such a sensitive and delicate product.
Steiner-Ukraine works with several manufacturers of this type of pump, each of which has its own characteristics and advantages for a particular process. We will be happy to study and solve any of your pumping tasks.