Cam pumps are used in a variety of industries, including pulp and paper, chemical, food, pharmaceutical and biotechnology. This type of pump is popular in these various industries due to its excellent sanitary qualities, high efficiency, reliability, corrosion resistance and good adaptation to CIP washing and SIP sterilisation.
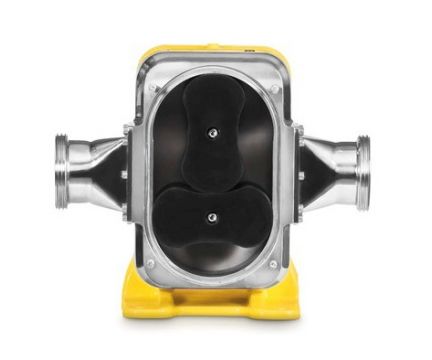
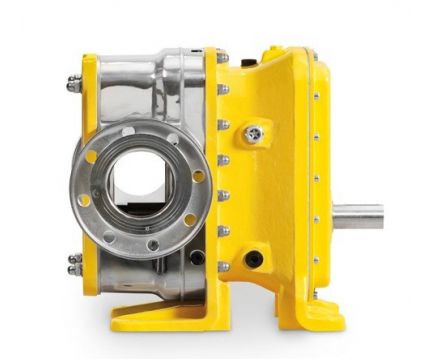
These pumps are available in a variety of rotor designs: single, double, triple and multi-vane. The cam pumps operate without engaging/contacting functional elements and have large working chambers. This makes it possible to pump products with solid particles without damage, such as yoghurts with fruit pieces, whey and curd mixtures, sauces with vegetables, etc. If the pump is filled with liquid and the impellers are wet, there is also self-priming ability. The gentle and gentle operation of the pump minimises the risk of damaging the product. Reverse operation and dry running for a long period of time are available as additional options. The flow rate is relatively independent of pressure changes, so it can be assumed that the cam pump delivers a constant and continuous flow.
According to the design, cam pumps can be divided into industrial and hygienic. The hygienic design is determined by the service and specific sanitary requirements. These requirements include compliance with various Type 3-A, EHEDG and FDA standards.
How does the cam pump work?
Cam pumps are similar to gear pumps in that the fluid moves along the rounded inside of the casing. The only difference is that in a cam pump, the rotors do not come into contact with each other, but engage and transmit rotation earlier through the gears in the gearbox. The bearings of the support shaft are located in the gearbox, and as they are not immersed in the pumped liquid, the pressure on them is limited by the positioning and deflection of the shaft.
- As the rotors move out of the gaps, they increase the volume at the inlet of the working chamber. The product moves/suctioned into the liquefaction zone and is picked up by the rotating rotors.
- The pumped medium moves along the inside of the casing in pockets between the rotor and the casing wall - it does not pass between the cams.
- As a result, the pumped medium is discharged under pressure through the outlet port by the cam forces.
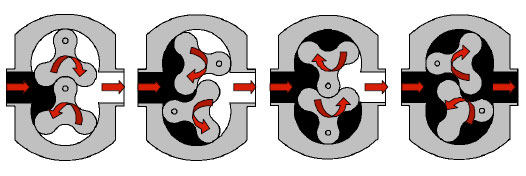
Cam pumps are often used in the food industry as they transport delicate products/products with pieces without damage. Here, the size of the particles to be pumped can be much larger than with other positive displacement pumps. Since the rotors do not come into contact with each other and the gaps between the working parts are slightly larger than with other positive displacement pumps, the efficiency with low-viscosity liquids is therefore lower. The load characteristics are not as good, and the self-priming ability is low. Pumping high-viscosity products requires a low rotational speed (typically 25% of the nominal speed) to achieve optimum performance.
Advantages and disadvantages:
The advantages include the following indicators:
- particle transfer without damage;
- no metal-to-metal contact between the working parts;
- good resistance to CIP cleaning and SIP sterilisation;
- possibility to work "dry" in the presence of mechanical seals with flushing
- pulsation-free feeding
Disadvantages:
- availability of an additional gearbox
- two mechanical seals (wearing parts)
- poor pressure characteristics in low-viscosity liquids
Boyser cam pumps (Spain)
The market for cam pumps is quite rich in the variety of suppliers of this type of equipment. When choosing a manufacturer, our company was guided by the current trends and needs of the Ukrainian market. After the analysis, we negotiated and reached a cooperation agreement with Boyser (Spain).
The main features of Boyser cam pumps:
- the entire range is focused on hygienic design and use in the food/pharmaceutical industry
- all contact parts are made of AISI 316L stainless steel with a surface finish of 0.8 µm
- the standard version includes DIN 11851 ports, a single mechanical seal and three-lobe cams;
- as an option, the pumps are available with other types of connections, heating jacket, enlarged rectangular inlet, different cam profile, etc.
- the performance range of the model range is shown in the figure below
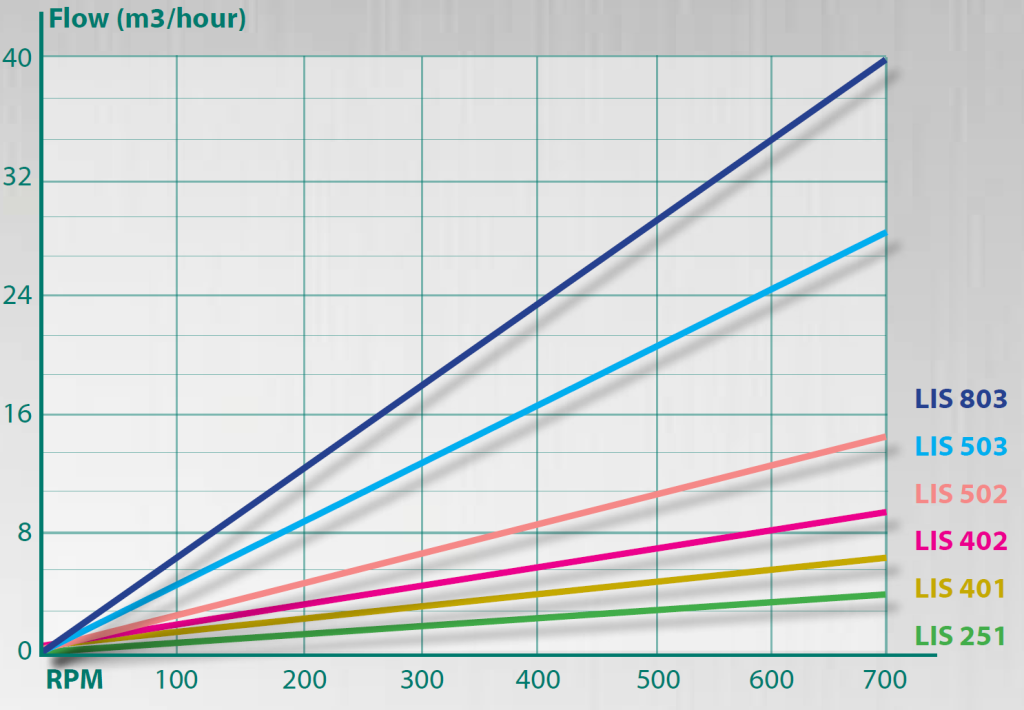
A separate branch of the product range is the rubberised rotor cam pump, which is characterised by higher self-priming capacity and abrasion resistance. These pumps have a more industrial design, but can also be used in the food industry.
Boyser's technical solutions are technologically advanced products with a good price-performance ratio. If you have any questions or need more information, please contact our technical specialists. We will find the best solution for you!