Chemical pump - series made of plastic
General characteristics of the NP series pump:
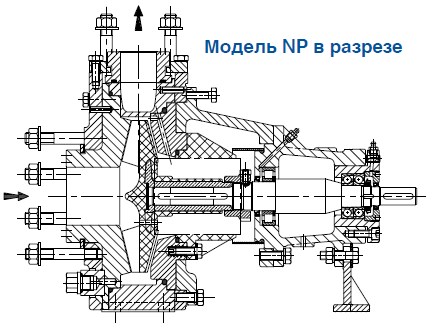
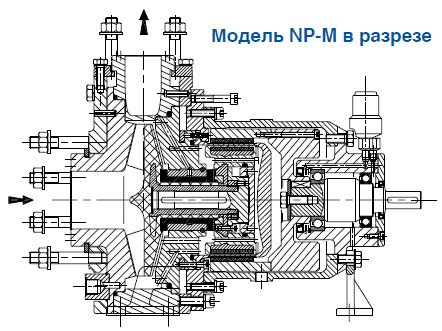
The centrifugal monobloc pumps of the NP series are designed for pumping corrosive clear or slightly turbid liquids in a wide variety of industries.
Standardisation:
The dimensions and specifications of the NP series pumps comply with NFE 44121 to DIN 24256.
- ISO 2858 and 5199. The NP pumps are designed for intensive use in the most demanding environments.
NP-M with electromagnetic drive:
They differ from conventional pumps in that they are absolutely leak-proof: thanks to the electromagnetic drive, there is no shaft seal. They meet the following standards:
- Machinery Directive 98/37/EC Annex II A
- Electromagnetic Compatibility Directive 89/336/CEE Annex I
- Low Voltage Directive 73/23/EEC Annex III B
Performance charts for chemical pumps:
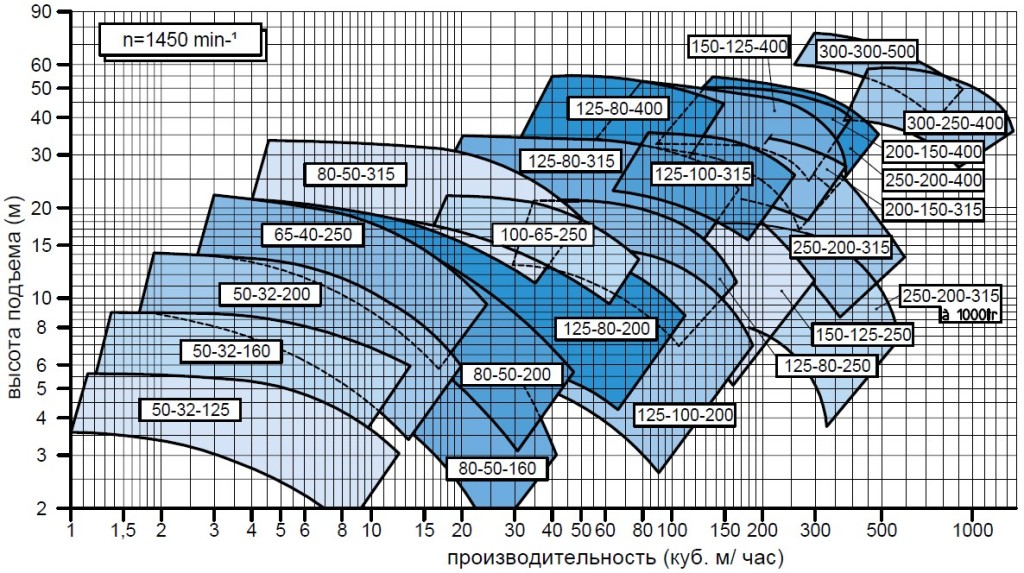
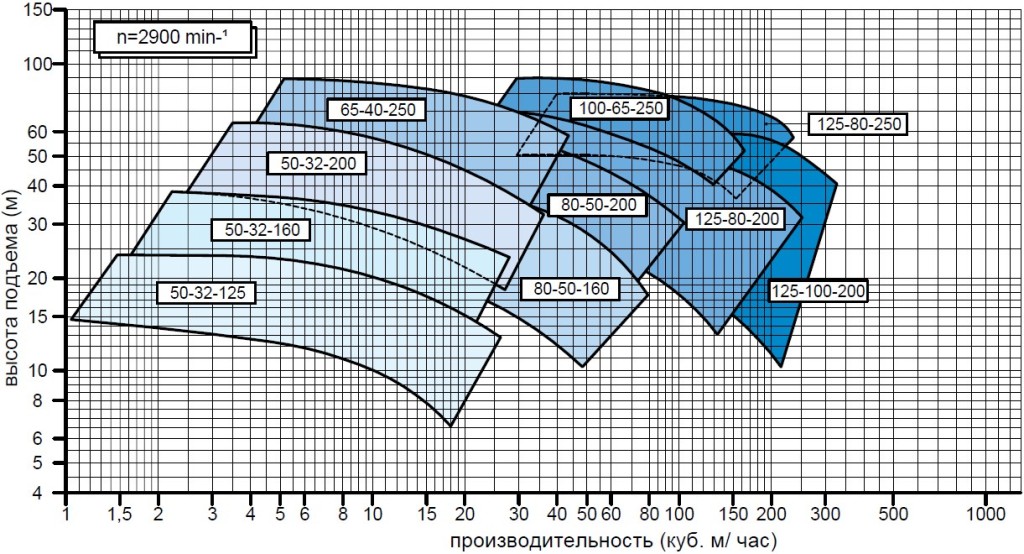
Versions of centrifugal chemical pumps:
NP-V / HV
The pumps of this series are designed for pumping highly abrasive liquids and liquids with a high content of suspended solids.
The HV series pumps are equipped with a tangential outlet snail and a vortex wheel to allow solids to pass through.
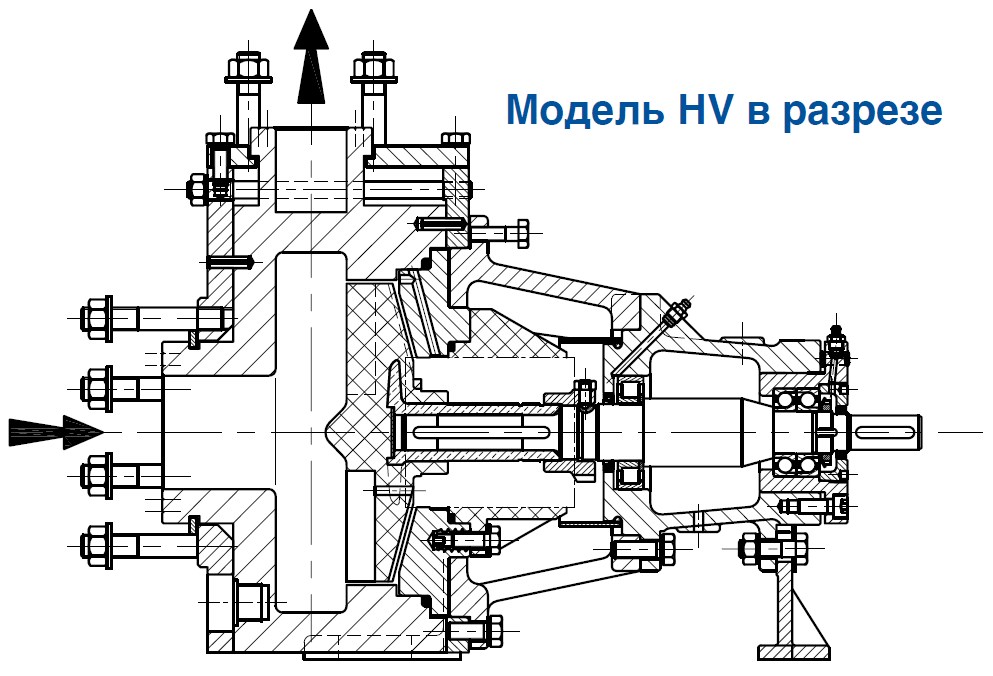
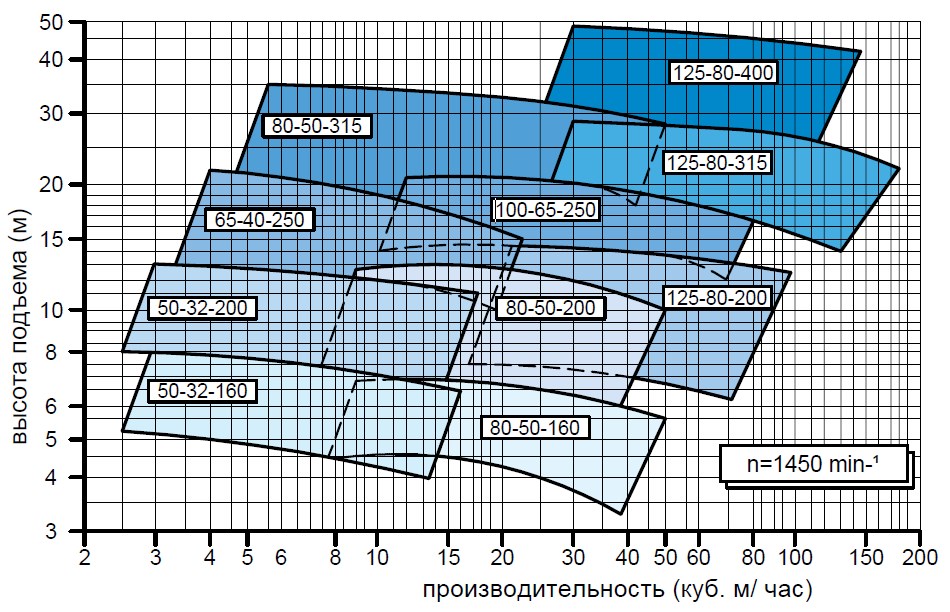
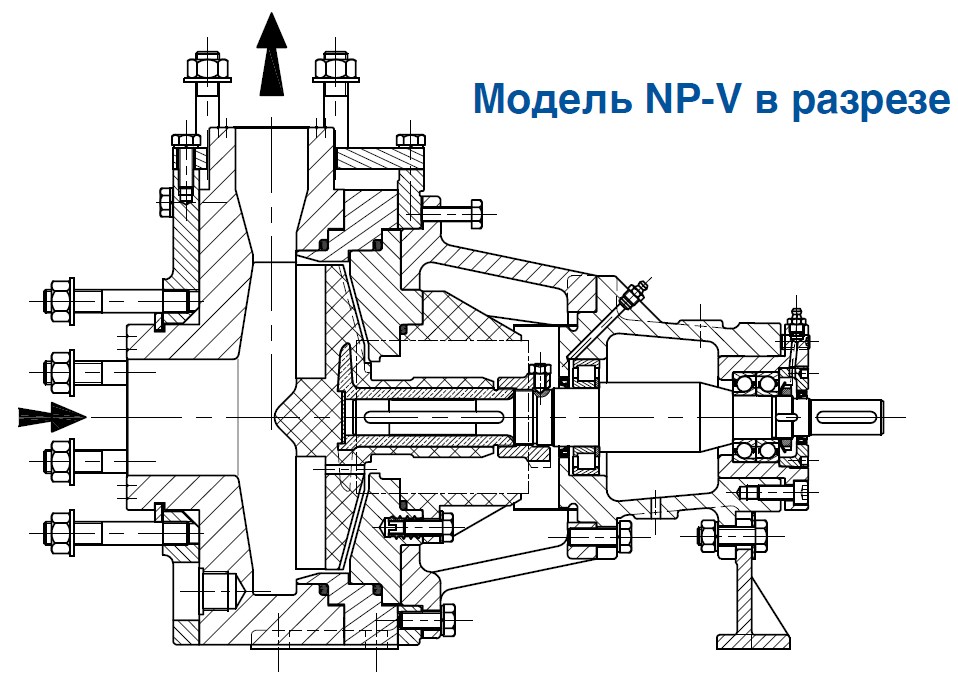
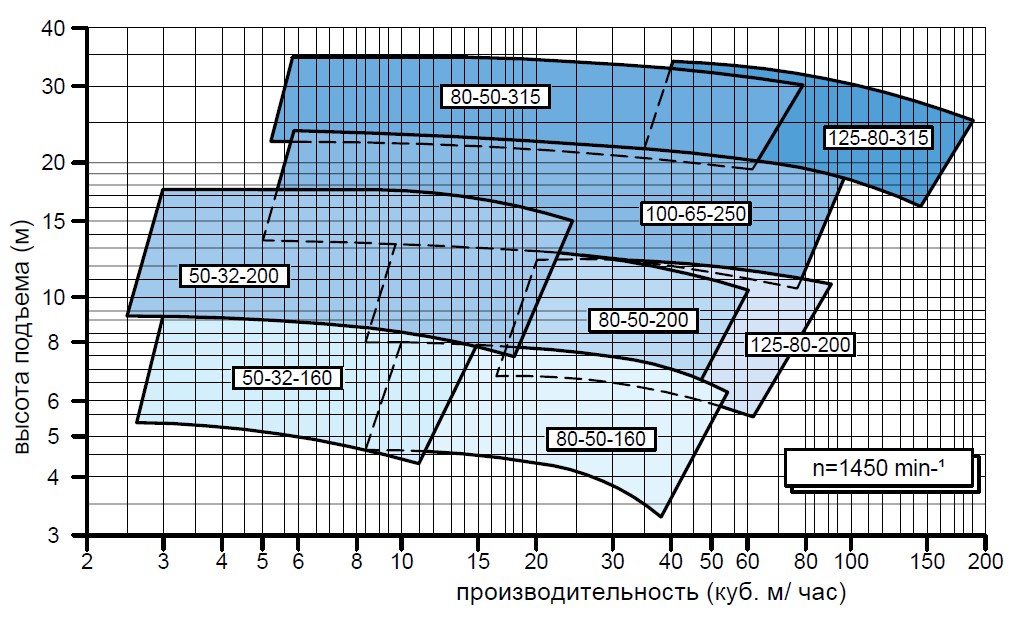
Monoblock pumps:
All NP, NP-M, NP-V and HV pumps can be implemented as a monoblock design with a power output of up to 15 kW, depending on the operating conditions.
ATEX compliance:
NP pumps and their variants can be supplied with ATEX 94/9/CE certification.
Voluntary certification INERIS 04 ATEX 3008X
Materials of construction of chemical pumps:
The hydraulic part is made entirely of heavy-gauge plastic parts.
No mechanical parts come into contact with the working fluid.
- Polypropylene PP or PP-EL
- PE-HD or PE-EL polyethylene
- PVC
- PVDF or PVDF-EL
- PTFE
- PFA
- SOMEDUR for abrasive liquids
- SOMEFLU for turbid corrosive liquids up to 90°C.
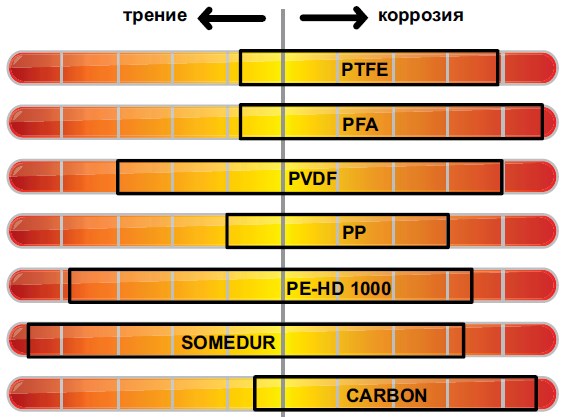
Mechanical seal with cartridge:
The shaft is sealed by a mechanical seal with a cartridge developed by SOMEFLU. This seal is factory-adjusted. It facilitates installation and maintenance operations. Depending on the nature of the fluid and the type of process, the seal can be implemented in the following variants:
- Rinsing with crystallised or turbid liquids stopped
- Injecting clean fluid into liquids containing abrasive materials. If the process allows, pure water can be used
- Sealing of the seal chamber with grease lubricant to limit the crystallisation effect if the process does not allow the inlet of clean water
- Double mechanical seal with external lubrication for hazardous or turbid liquids
Насос із нержавіючої сталі використовують для перекачування агресивних і корозійних рідин у хімічній, фармацевтичній та харчовій промисловості.
Він відзначається високою стійкістю до корозії, довговічністю та надійністю в складних умовах експлуатації.
Вибір залежить від типу рідини, температури, тиску і технологічних вимог. Наші фахівці допоможуть зробити правильний вибір.
Компанія Штайнер пропонує оригінальні насоси з нержавіючої сталі з офіційною гарантією і доставкою по Україні.
Так, ми забезпечуємо ремонт, обслуговування і постачання оригінальних запчастин для цих насосів.